Automotive design has always been a race—faster production, lighter components, smarter systems. But in recent years, a new kind of race has emerged, not on the track but in the factory: the competition to reimagine how cars are made. At the heart of this transformation is 3D printing, or additive manufacturing. No longer just a prototyping tool, it’s now reshaping the way vehicles are conceptualized, engineered, and brought to life.
3D printing in the automotive sector refers to the process of fabricating parts layer by layer using digital models, allowing for highly customized, complex components to be produced faster and more efficiently than with traditional manufacturing methods. Whether you’re prototyping or scaling low-volume production, choosing the right 3D printer for automotive parts is key to unlocking both design flexibility and functional performance.
In this guide, you’ll learn how 3D printing is shifting the dynamics of car part production, what technologies and materials are leading the charge, and where this evolution is heading next. From design freedom to electric vehicle innovation, we’ll unpack the full impact of additive manufacturing on tomorrow’s mobility.
How is 3D printing changing vehicle design today?
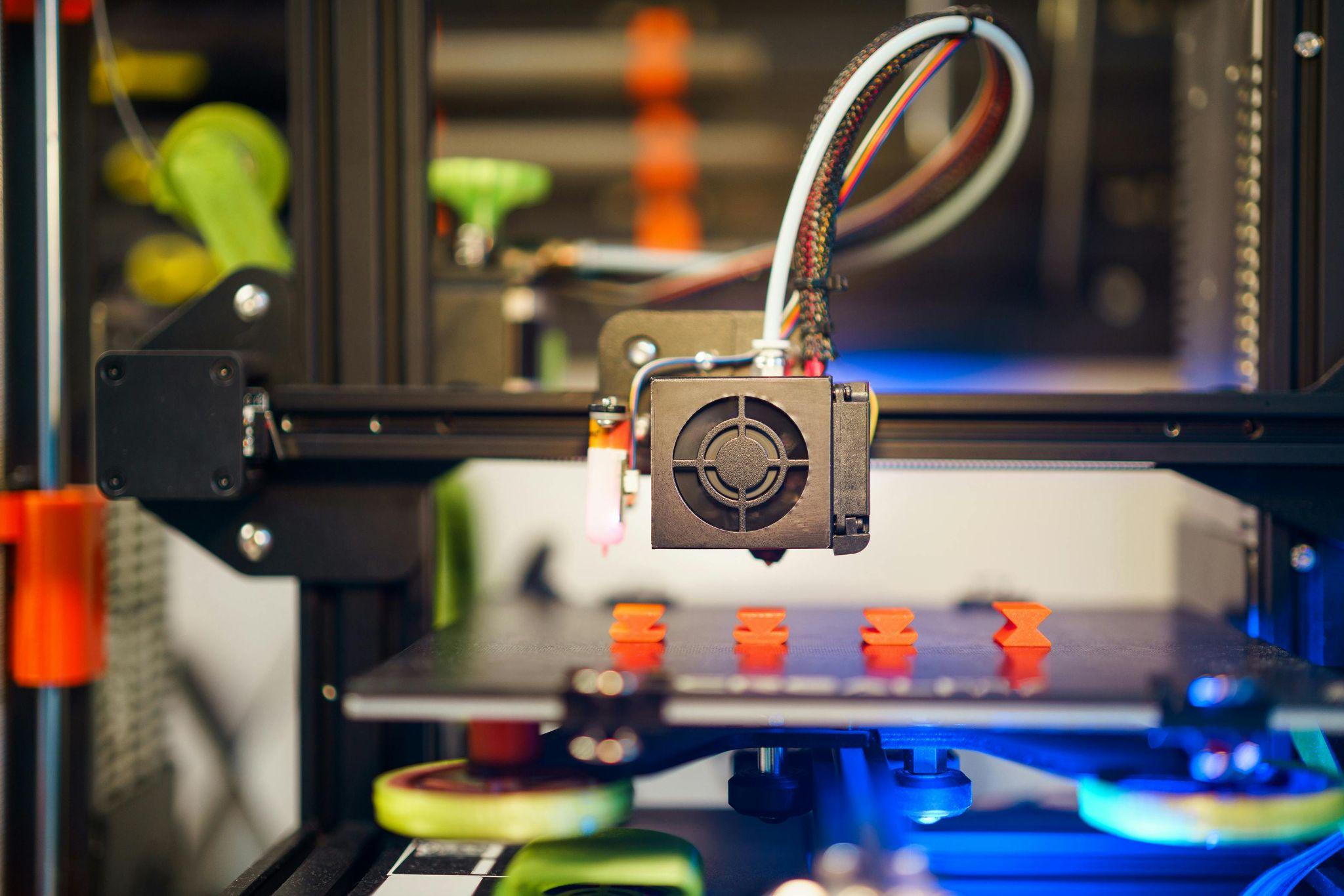
When engineers move from subtractive to additive thinking, the rules of automotive design change dramatically. 3D printing removes long-standing limitations, enabling geometries that were once considered impossible. Complex internal lattices, consolidated assemblies, and form-fitting shapes are now achievable at scale, opening up new performance horizons.
This shift isn’t just technical—it’s cultural. Traditional manufacturing relied on constraints like mold design, draft angles, and machining paths. In contrast, additive manufacturing empowers teams to optimize parts for function first, not fabrication. Lighter, stronger, and smarter parts are the result.
Major automakers have already adopted this philosophy. General Motors used 3D printing to develop a seat bracket that consolidated eight components into one, cutting weight by 40%. BMW has printed thousands of roof braces for its i8 Roadster, while Ford relies on additive technologies for brake components, fluid ducts, and even end-use tools across production lines. These aren’t lab experiments—they’re real-world applications reshaping how cars get built.
What automotive parts are commonly 3D printed?
From dashboards to drivetrain supports, additive manufacturing is touching every corner of the modern vehicle. But not all parts serve the same role—or require the same materials.
Typical applications include:
Interior Components
- Material: Thermoplastics like ABS, TPU
- Purpose: Custom knobs, HVAC ducts, aesthetic trims
- Use Case: Prototyping and low-volume end-use
Under-the-Hood Parts
- Material: Nylon composites, carbon fiber-reinforced polymers
- Purpose: Engine mounts, brackets, fluid routing components
- Use Case: Functional testing and limited production
Chassis and Structural Elements
- Material: Aluminum alloys, stainless steel
- Purpose: Support brackets, frame connectors
- Use Case: Tooling fixtures, pilot production
Tooling and Jigs
- Material: High-performance thermoplastics (e.g., ULTEM)
- Purpose: Assembly jigs, custom measurement tools
- Use Case: Factory floor operations and validation
Each category benefits differently, but together they highlight how additive manufacturing is spreading far beyond simple prototypes.
What are the main benefits of using 3D printed parts in vehicles?
Additive manufacturing offers a powerful blend of speed, precision, and agility. Here’s how those advantages translate in practice:
- Weight Reduction – Complex lattice structures reduce material use without sacrificing strength.
- Faster Prototyping Cycles – Rapid iterations accelerate R&D timelines and testing.
- Tool-less Manufacturing – Eliminates the need for costly molds or dies.
- Cost Savings in Low-Volume Production – Ideal for niche vehicles or spare parts.
- Enhanced Geometric Complexity – Enables parts with internal channels, honeycombs, and topology optimization.
- Customization and Personalization – Supports unique trims, driver-specific controls, or luxury accents.
- Reduction in Assembly Steps – Consolidates multi-part assemblies into a single printed component.
These gains are especially valuable in electric vehicles and performance cars, where weight, time, and integration are critical.
What are the limitations of 3D printing for automotive use?
Despite its promise, additive manufacturing has constraints that must be considered during development. Some challenges are technological; others are regulatory.
Common limitations include:
- Limited Material Strength for High-Stress Parts – Not all 3D printed materials match the fatigue or impact resistance of forged metal.
- Surface Finish Quality – Often requires post-processing for aesthetic or aerodynamic needs.
- Long Build Times for Large Components – Complex parts can take hours—or days—to print.
- Post-Processing Requirements – Supports must be removed, surfaces finished, and parts inspected.
- Regulatory Hurdles for Road-Ready Parts – Certification can be time-consuming and complex for safety-critical components.
Still, many of these issues are actively being addressed as hardware, materials, and standards evolve.
What types of 3D printing technologies are used in the automotive industry?
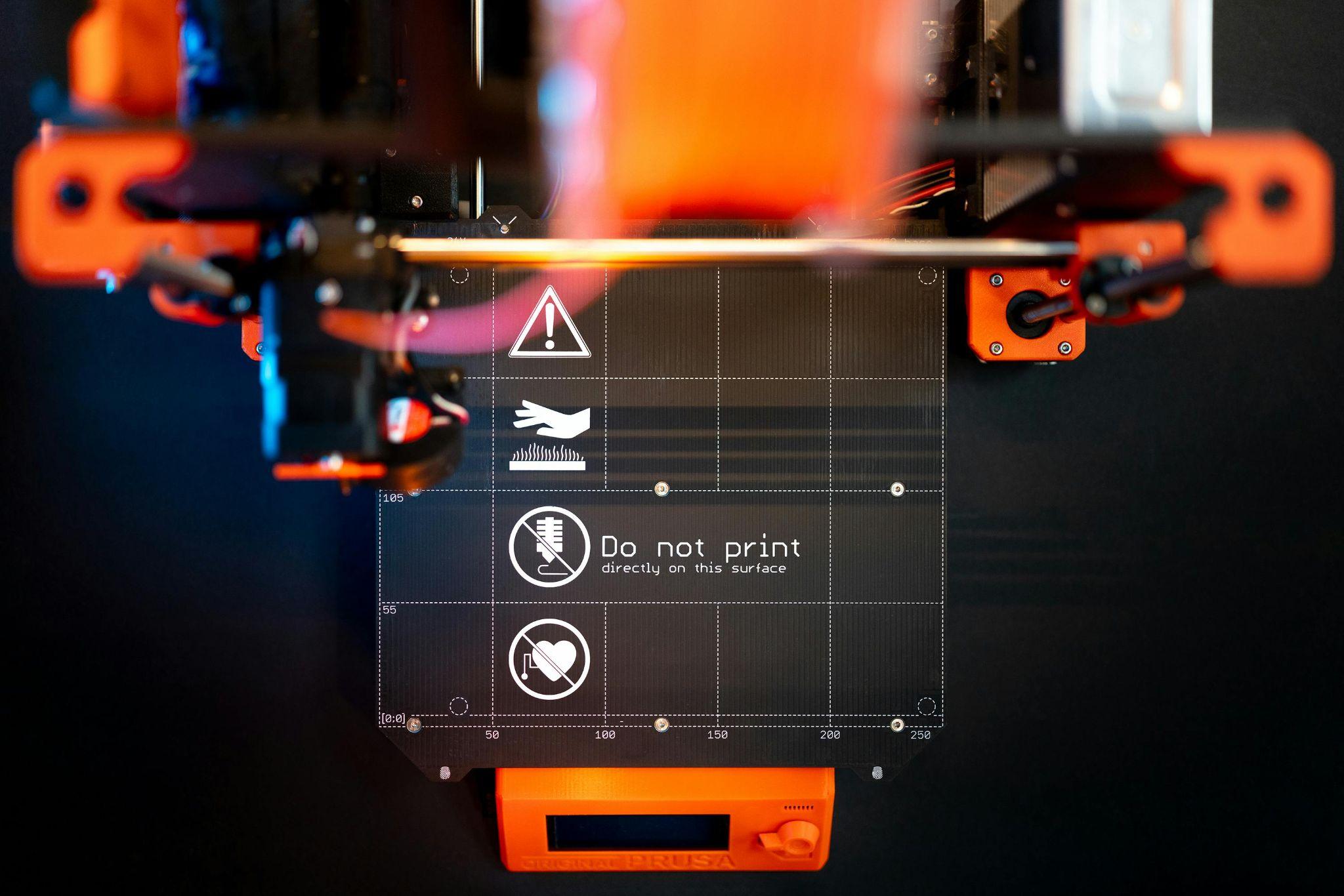
The auto sector uses a wide range of additive processes depending on the application, material, and part complexity. Understanding the different 3D printing types is essential for selecting the right approach—whether it’s prototyping, tooling, or producing functional components.
Fused Deposition Modeling (FDM)
How it works: Layers melted filament through a heated nozzle.
Pros: Cost-effective, fast for prototypes.
Cons: Lower resolution and weaker mechanical properties.
Stereolithography (SLA)
- How it works: Uses UV light to cure liquid resin.
- Pros: High-detail surface finish, ideal for concept models.
- Cons: Brittle parts not suitable for load-bearing functions.
Selective Laser Sintering (SLS)
- How it works: Fuses powder particles layer by layer using a laser.
- Pros: Strong, functional nylon parts; no support structures needed.
- Cons: Rougher surface finish, more expensive than FDM.
Direct Metal Laser Sintering (DMLS) / SLM
- How it works: Laser fuses metal powders in high precision.
- Pros: Produces fully functional metal components.
- Cons: Expensive equipment and complex post-processing.
Binder Jetting
- How it works: Binds powder material using a liquid adhesive, then sinters.
- Pros: Good for large metal batches, fast print speed.
- Cons: Lower mechanical strength than DMLS.
Multi Jet Fusion (MJF)
- How it works: Fuses powder using fusing and detailing agents.
- Pros: High speed, good strength and detail.
- Cons: Limited to polymers.
Which materials are used for 3D printed car parts?
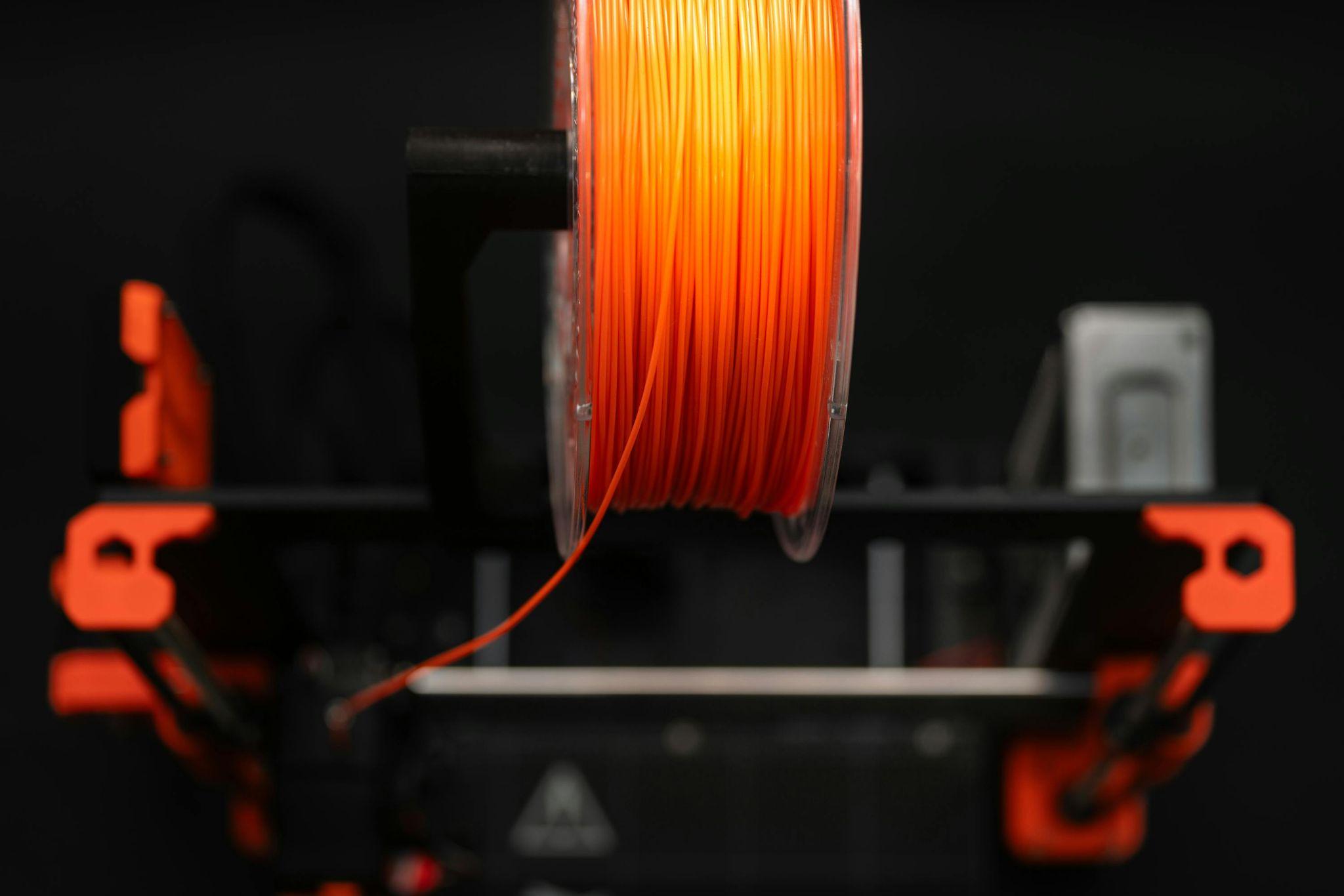
Material selection depends on the part’s purpose—structural, cosmetic, or functional. Below is a breakdown of typical choices:
Thermoplastics
- Examples: ABS, Nylon, ULTEM
- Attributes: Moderate strength, temperature-resistant, durable
- Use: Prototypes, enclosures, ducts
Composite Filaments
- Examples: Carbon fiber or glass-filled polymers
- Attributes: Enhanced stiffness, lightweight
- Use: Mounts, brackets, structural supports
Photopolymers
- Examples: Epoxy-based resins
- Attributes: High detail, low strength
- Use: Aesthetic models and design validation
Metals
- Examples: Aluminum, Titanium, Stainless Steel, Inconel
- Attributes: High strength, corrosion-resistant, high-temp tolerance
- Use: End-use mechanical parts and performance components
How do 3D printed parts compare to traditional manufacturing?
3D printing flips conventional trade-offs on their head. While traditional processes like injection molding and CNC machining dominate high-volume production, additive manufacturing excels in flexibility, customization, and design innovation.
Key comparison factors include:
- Speed: Faster for prototyping, slower for large volumes
- Cost: Lower tooling costs; higher per-part cost for mass runs
- Design Complexity: Unmatched freedom with internal features and topology
- Strength: Competitive for some applications; metals rival machined parts
- Volume Suitability: Ideal for one-offs to low-volume batches
- Sustainability: Less waste, but energy consumption varies by process
Designers often blend both approaches—printing prototypes and complex geometries, while machining standard, high-volume elements.
What role does 3D printing play in vehicle prototyping?
Additive manufacturing dramatically shortens the path from digital model to physical test part. Engineers can validate design intent, test fit, and assess function without waiting for tooling or machining.
Common prototyped parts include:
- HVAC ducts for airflow studies
- Instrument panels for ergonomic testing
- Engine covers for thermal validation
- Mounting brackets for stress simulations
By enabling same-day iterations, 3D printing turns design loops into design sprints.
Can 3D printed parts be used in final production vehicles?
Yes—and they already are. While prototyping remains the primary use, production-grade 3D printed parts are showing up in both consumer and motorsport vehicles.
Visible examples include customized interior panels and vent trims. Hidden parts like cooling ducts, wire harness brackets, and sensor housings are also commonly printed. These components undergo fatigue, thermal cycling, and crash simulations to meet homologation standards.
Ford, Bugatti, and Porsche have all integrated functional, printed parts directly into vehicles sold to customers.
How does 3D printing support electric vehicle (EV) development?
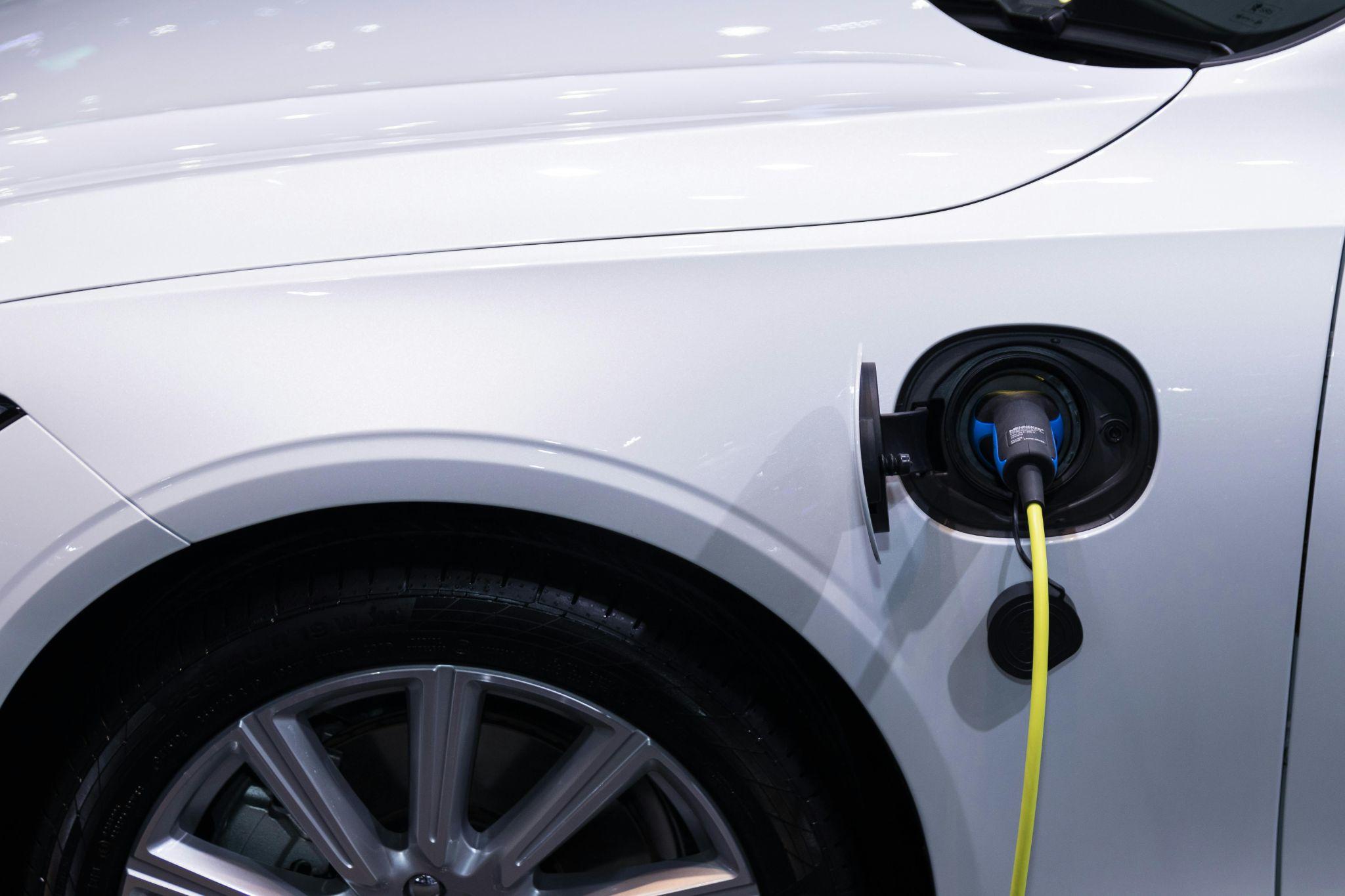
EVs demand lightweight structures, efficient cooling, and flexible packaging—all areas where additive manufacturing excels.
Frequently printed EV components include:
- Battery cooling channels and manifolds
- Lightweight enclosures and shields
- Custom wire harness clips and guides
- Thermal interface fixtures and airflow ducts
Reducing part count and weight has a direct impact on EV range and efficiency—key metrics in today’s electric car race.
How are car manufacturers integrating 3D printing into their workflows?
Manufacturers use a mix of centralized hubs and distributed print farms. BMW’s Additive Manufacturing Campus consolidates R&D, prototyping, and small-batch production in one location. Meanwhile, Ford and GM deploy desktop printers across factory floors to produce jigs, tools, and fixtures in real-time.
Collaborations also play a major role. Volkswagen has partnered with HP for polymer production and Siemens for digital workflow integration. Service bureaus like GKN Additive and Materialise provide overflow capacity and metal part expertise.
This hybrid approach ensures speed, scalability, and repeatability.
What are the most important design rules for automotive 3D printing?
Designing for additive isn’t the same as designing for injection molding or machining. To take full advantage, engineers follow specific DfAM principles.
Key guidelines include:
- Maintain consistent wall thickness to reduce warping
- Avoid unsupported overhangs that require extra scaffolding
- Use fillets instead of sharp edges to distribute stress
- Orient parts to optimize layer adhesion and mechanical strength
- Design threads and joints with post-processing in mind
- Account for tolerances and cleanup in critical dimensions
Designing smart ensures functional, cost-effective prints from the first iteration.
What quality standards and certifications apply to 3D printed car parts?
As 3D printing moves into production, quality assurance is catching up. Standards help ensure consistency, safety, and compliance across suppliers and OEMs.
- ISO/ASTM 52900 defines terminology and process classification
- IATF 16949 aligns with broader automotive quality requirements
- Testing protocols include fatigue analysis, tensile strength, crashworthiness, and thermal performance
Meeting these standards is essential for parts that affect driver safety or system reliability.
What are the environmental impacts of 3D printing in automotive?
3D printing’s sustainability profile is nuanced. While it reduces material waste, energy use and recyclability vary by technology and material.
Key sustainability considerations:
- Reduced material waste versus machining
- On-demand production lowers inventory and storage needs
- Supports localized supply chains, reducing shipping emissions
- Energy consumption can be high, especially for metal processes
- Limited recycling options for some polymers and resins
Still, it offers a pathway to more efficient, lighter, and purpose-built vehicles.
What’s next for 3D printing in vehicle design and manufacturing?
Looking forward, 3D printing is poised to expand from the periphery to the core of automotive workflows.
Emerging trends include:
- Larger-format metal printers capable of structural components
- Tighter integration with generative design and AI optimization tools
- In-line quality monitoring during the print process
- Growth in full-scale production, not just prototyping or tooling
With every advancement, the boundary between concept and production narrows.
Conclusion
3D printing has outgrown its roots in prototyping to become a cornerstone of modern vehicle development. From interior panels to metal brackets, it’s changing how parts are conceived, validated, and delivered. By enabling lighter designs, faster iterations, and unprecedented design freedom, it’s not just keeping pace with automotive innovation—it’s driving it.
And as electric vehicles, personalization, and on-demand production accelerate, so will the role of additive manufacturing in shaping what we drive next.